Programm

Eröffnung
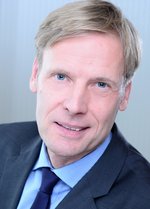
Dr. Frank Schröder-Oeynhausen
Technikzentrum Lübeck
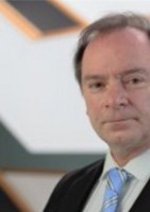
Prof. Dr. Thorsten Buzug
Fraunhofer Research Institution for Individualized and Cell-Based Medical Engineering, Lübeck Universität zu Lübeck, Institut für Medizintechnik
Grußworte
Abteilungsleiter Johannes Hartwig
- Ministerialdirigent -
„Technologie, Tourismus und Marketing“
Ministerium für Wirtschaft, Verkehr, Arbeit, Technologie und Tourismus des Landes Schleswig-Holstein

Keynote 1: Industrielle Additive Fertigung - aktuelle Potentiale und Herausforderungen
Moderation: Dr. Frank Schröder-Oeynhausen
Technikzentrum Lübeck, Germany
Abstract: Additive Fertigungsverfahren haben nach dem Ende des "Hype" ihren Weg in Richtung einer robusten Industrialisierung angetreten. Doch ist es nicht selbstverständlich, dass sich durch Umstellung der Fertigungsverfahren in Richtung "Additiv" auch Geld verdienen lässt. Wenn man einige wesentliche Punkte beachtet, kann es aber gelingen. Der Keynote Vortrag gibt eine Übersicht über die industriell wichtigsten Verfahren und einige "lessons learnt" zu den Themen Implementierung, Zulassung und Business Case.
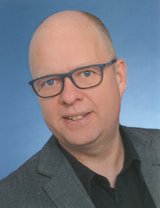
Jens Telgkamp arbeitete nach dem Studium des Maschinenbaus in Braunschweig und der Promotion im DFG Graduiertenkolleg "Kontinuumsmechanik Inelastischer Festkörper" (2001) bei der Airbus Operations GmbH in Hamburg und Toulouse in verschiedenen Bereichen, darunter Statik, Konstruktion/Design und Forschung, unter anderem als "Head of Fuselage Structure Design". Seine letzte Aufgabe bei Airbus war die Leitung der Forschungsaktivitäten rund um Additive Fertigungstechnologien als "Head of AM Research&Technology". Seit September 2019 ist Jens Telgkamp Professor für Produktionstechnik / Additive Fertigung an der HAW in Hamburg.

Session 1: Metalldruck und Qualitätssicherung
Moderation: Dr. Thomas Friedrich
Fraunhofer Research Institution for Individualized and Cell-Based Medical Engineering, Lübeck, Germany

Industrialisierung der metallbasierten additiven Fertigung: Vom Prototyping zur Serienproduktion
Hendrik Schonefeld, Head of Sales EMEA, SLM Solutions Group AG
Abstract: Kontinuierliche Produktivität ist ein grundlegender Bestandteil von AM-Systemen und in den letzten Jahren gab es eine erhebliche Produktivitätssteigerung bei selektiven Laserschmelzsystemen. Diese Steigerung beruht auf dem Einsatz von Multi-Lasersystemen in Kombination mit größeren Installationsvolumina und höherer Laserleistung. Um eine höhere Produktivität und Serienfertigung zu erreichen, konzentriert sich das Multi-Laser-SLM®-Verfahren vor allem auf die Faktoren Produktionskosten, Teilequalität und Zuverlässigkeit.
In diesem Vortrag werden die relevanten technischen Entwicklungen, die Auswirkungen auf die wichtigsten Produktionsfaktoren und deren Zusammenwirken sowie die wirtschaftlichen Vorteile behandelt. Die Auswirkungen dieser Entwicklungen auf die Teiledichte, die mechanischen Eigenschaften der Teile und die Baugeschwindigkeit werden untersucht. Fallstudien aus verschiedenen Industrien werden aufgezeigt und untermauern den wirtschaftlichen Einsatz von Multi-Laser-SLM®-Maschinen für die qualifizierte Serienproduktion.
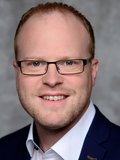
Hendrik Schonefeld begann nach seinem Maschinenbaustudium an der Technischen Universität Hamburg-Harburg (Deutschland) seine berufliche Laufbahn bei dem international tätigen Unternehmen Jungheinrich AG. In seiner mehrjährigen Tätigkeit als Projektleiter - Entwicklungsabteilung führte er mehrere Projekte zum erfolgreichen Abschluss. Während dieser Zeit verlor er den Kontakt zu seiner Alma Mater nicht. Diese kontinuierliche Beziehung führte zu einem Stellenangebot des LZN - Laser Zentrum Nord, einer Ausgründung der Technischen Universität Hamburg-Harburg, die als Forschungszentrum für industrielle Anwendungen auf dem Gebiet der Lasertechnik fungiert. Hendrik nutzte die neue Chance und wurde Leiter der Mikroabteilung mit dem Schwerpunkt Selective Laser Melting und Laserablation. In dieser Funktion war er für das technische Management, den Vertrieb und das Marketing sowie für die Mitarbeiterführung verantwortlich. Nach einer kurzen Pause als Vertriebsleiter im Bereich kundenspezifischer automatischer Montagelinien nahm Hendrik ein Angebot der SLM Solutions in Lübeck (Deutschland) an und übernahm die flächendeckende Vertriebsverantwortung für die SLM® Technologie. Zunächst als Regional Sales Manager trieb er den Vertrieb und die Marktentwicklung in Nordeuropa voran. Seit Anfang 2017 ist er als Head of Sales für die Region EMEA verantwortlich.

Bessere Lösungen für Betriebsmittel durch 3D-gedruckte Metallteile
Matthias Winderlich, AM Metals GmbH
Abstract: AM Metals ist Teil der EOS-Gruppe und steht für „Additive Manufacturing“ von Metallen, häufig auch 3D-Druck genannt. Dabei entstehen Bauteile für Betriebsmittel, insbesondere für Automationsanlagen, Vorrichtungen und Werkzeuge direkt aus Konstruktionsdaten (CAD) und Metallpulver. 3D-Druck ermöglicht die Individualisierung der Kundenapplikation z.B. als konturbasierte Teile für Spannvorrichtungen und Werkzeuge, Werkstückträger/Carrier sowie Greifer oder Applikationswerkzeuge für Roboter oder der hochfeste Strukturteile im Leichtbau. Der Vorteil aller von uns hergestellten Teile ist die Funktionsintegration, welche eine Vielzahl von Anforderungen auf engstem Raum in nur einem Bauteil vereint. Solche Teile gelten eigentlich als nicht herstellbar. Diese Grenze verschieben wir gerade bei den Betriebsmitteln. Ergänzt wird dies durch innovative Werkstoffe wie hochfeste Werkstähle sowie das innovative Aluminium AlFe-HT, was auch bei Dauertemperaturen bis 300 °C hohe Festigkeiten bewahrt.
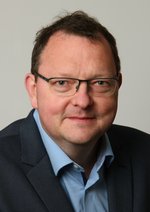
Aktuell tätig als Vertriebsingenieur im Bereich Geschäftsfeldentwicklung bei der AM Metals GmbH.
Nach einer Ausbildung in der MSR -und Steuerungstechnik folgten Betriebswirtschaft und Maschinenbau über den zweiten Bildungsweg. Ergänzt wird dies durch eine Mitarbeit in regionalen und Branchennetzwerken sowie Standardisierungsgruppen.
Ein umfangreiches know-how und langjährige Erfahrungen wurde im Mittelstand begründet, wo in der Rolle eines Generalisten komplexe Themen strukturiert und gelöst worden sind. Dazu zählen u.a.
- 15 Jahre Markterschließung, Vertrieb und Projektmanagement von speziellen technologischen Lösungen im Bereichen Werkzeugmaschinen für die Präzisions- und Großteilbearbeitung
- 6 Jahre Projektmanagement und strategischer Einkauf zur Industrialisierung von automatisierten physikalischen und chemischen Prozessen in der Solarzellherstellung
- 4 Jahre Geschäftsfeldentwicklung für die Anwendung additiver Verfahren zur Teilefertigung

Qualitätsinspektion von 3D gedruckten Teilen
Lennart Schulenburg, Commercial Director, VisiConsult X-ray Systems & Solutions GmbH
Abstract: Das Verfahren der additiven Fertigung (AM) hat sich zu Verfahren für die Produktion von Bauteilen mit anspruchsvoller Bauteilgeometrie entwickelt. Auf Grund der Fertigungsweise haben sich neue Herausforderungen bezüglich der Prozesskontrolle, Qualitätssicherung sowie Oberflächenbearbeitung ergeben, bei deren Lösung die Computertomographie (CT) als Sensor einen wertvollen Beitrag liefern kann.
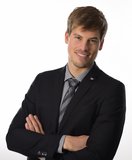
Lennart Schulenburg ist Branchenvisionär und kaufmännischer Leiter beim Röntgeninnovator VisiConsult. Er initiiert erfolgreich aufschlussreiche Kooperationsforschungen und spricht regelmäßig auf Branchenveranstaltungen über die neuesten Trends und Innovationen. Sein Motto "Es ist nie ein Problem, sondern eine Herausforderung" unterstreicht deutlich seine Begeisterung. Vor 30 Jahren wurde VisiConsult von seinem Vater gegründet und entwickelt kontinuierlich neue Röntgenlösungen, um den Röntgenbedarf in den Märkten zerstörungsfreie Tests, Sicherheit und Elektronik zu decken.


Session 2: Kunststoffdruck und Anwendungen
Moderation: Dr. Frank Schröder-Oeynhausen
Technikzentrum Lübeck

Erfolgreicher Einstieg in den Desktop Metall 3D-Druck
Julian Milling, Application Engineer, IGO3D GmbH
Abstract: Additive Fertigung von Metallbauteilen ist häufig eine kostspielige und aufwendige Angelegenheit. Mittlerweile gibt es auch Desktopgeräte, die in der Lage sind Metallteile zu generieren. Die Hersteller haben ihre Anlagen weiterentwickelt und damit die Qualität der gedruckten Teile stetig verbessert. Auch die Software und Handhabung der Geräte haben einen deutlichen Sprung gemacht. Bedienerfreundlichkeit und Zuverlässigkeit stehen im Fokus der neuen Generation der Desktopdrucker. Das hat zur Folge, dass die Erfolgsquote steigt und weniger Nacharbeit notwendig ist. Die Nutzer können sich auf ihre eigentlichen Kompetenzen, wie z.B. Entwicklung oder Konstruktion, fokussieren.
Lange Zeit war das Generieren von Strukturen aus Metall den Pulverbettverfahren vorbehalten. Diese Anlagen sind kapitalintensiv und benötigen weitere Peripherie und haben dadurch hohe Einstiegshürden. Anschlüsse und Leitungen von Schutzgasen für eine inerte Atmosphäre in den Anlagen ist nur eine von vielen Voraussetzung. Das Pulverhandling bedarf auch besonderer Vorsichtsmaßnahmen, um die Arbeitssicherheit nicht zu gefährden.
Im Gegensatz dazu ist Metall-FFF ein Verfahren mit sehr niedrigen Einstiegshürden. Es benötigt lediglich einen Desktop 3D-Drucker und das Metallfilament. Die Geräte kosten einen Bruchteil von den Pulverbettanlagen und kommen komplett ohne Pulverhandling aus. Das Metallpulver ist in eine Bindermatrix aus Polymeren eingebettet und kann so einfach und sicher verarbeitet werden.
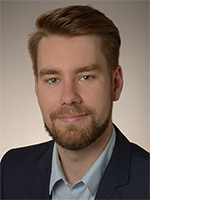
- M. Sc. Julian Milling
- Master Wirtschaftsingenieur TU Dresden
- 2 Jahre Forschung am Fraunhofer IWS in Dresden
- Parameterstudien FFF-Druck
- Funktionsintegration FFF-Bauteilen
- Bewertungsverfahren für Vergleich additiver Fertigungstechnologien
- Seit 2019 Application Engineer bei IGO3D
- Durchführung von Trainings und Webniaren
- Beratung bei Technologie- und Anlagenauswahl
- Identifikation und Umsetzung von Anwendungen im Bereich 3D-Druck

Ideale Bauteile zum Einstieg in den 3D Druck
EOS GmbH Electro Optical Systems
Abstract: Der 3D Druck ist eine faszinierende Technologie über die jeder spricht. Nur viele Fragen sich, wie kann ich die Technologie erfolgreich auch in der Serienfertigung einsetzen? Wir zeigen Ihnen wie Werkstücke, die bisher konventionell auf Fräsmaschinen gefertigt wurden nun erfolgreich auf 3D Druckern hergestellt werden. Durch Funktionsintegration, Wegfall von Montagearbeiten oder Wegfall der NC-Programmierung können enorme Einsparungen erzielt werden. Condor Custom Solutions und EOS zeigen anhand von Beispielen aus der Medizintechnik mit welchen Systemen, Materialien und Bauteilen der Weg vom Fräsen zum Drucken sehr erfolgreich gelingt.
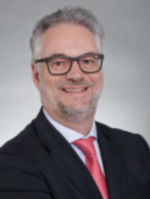
Ulf Flinspach ist bei EOS für den Vertrieb von additiven Fertigungssystem in Norddeutschland verantwortlich. Er betreut vorwiegend mittelständische Kunden, insbesondere berät er diese beim Einstiege in die additive Fertigung. Vor seiner Zeit bei EOS konnte er langjährig Erfahrungen mit Applikation und Vertrieb von Drehmaschinen und Bearbeitungszentren in Branchen wie z.B. Automotive, Maschinenbau oder Medizintechnik sammeln. Diese Erfahrungen kommen ihm besonders zu Gute wenn die Entscheidung ansteht, ob ein Werkstück konventionell oder additive gefertigt werden soll. Ulf Flinspach hat Maschinenbau an der Universität Kaiserslautern studiert.

Vom Prototyping zur Serienfertigung
Dominik Müller, Strategic Account Manager, Stratasys GmbH
Abstract: Erfahren Sie mehr über die Möglichkeiten der Additiven Fertigung und wie auch Sie, mit einem industriellen 3D-Drucker von Stratasys, Kosten und Zeit bei der Erstellung von Prototypen, Verbundwerkzeugen, Produktionsteilen und vielen weiteren Applikationen sparen können.
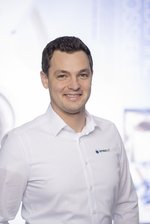
- Bachelor of Engineering in Industrial Engineering
- 4 Jahre Applications- & Sales Engineer: Evaluierung, Design for Additive und Beratung von Kunden in ganz EMEA aus den Bereichen Automotive, Aerospace, Medical, Konsumgütern und Prototyping
- Zuvor 4 Jahre bei Johnson Controls (Automobilzulieferer) für die Fahrzeugsitz-Produktion


Session 3: Digitalisierung und spezielle Verfahren
Moderation: Prof. Dr. Thorsten M. Buzug
Fraunhofer Research Institution for Individualized and Cell-Based Medical Engineering, Lübeck, Germany
Universität zu Lübeck, Institut für Medizintechnik

In 4 Schritten zur Additiven Fertigung
Christian Reinhardt, Business Development Manager, BASF 3D Printing Solutions GmbH
Die additive Fertigung ist für KMU’s von großem Nutzen, da sie Innovationszyklen verkürzen und Entwicklungskosten einsparen kann. Doch für viele Unternehmen ist der Einstieg in die additive Fertigung mit Herausforderung verbunden. Forward AM, die 3D Druck Sparte von BASF, bietet neben seinem einzigartigen Portfolio an 3D Druck Materialien auch ein umfangreiches Service Portfolio an. Durch diesen ganzheitlichen Ansatz und unser weitreichendes Partnernetzwerk, begleiten wir Sie von der ersten Idee bis zur gedruckten Applikation. In unserem Vortrag wollen wir unsere Expertise mit Ihnen teilen, um Ihnen den Einstieg in die additive Fertigung so leicht wie möglich machen.
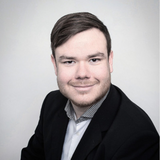
Christian Reinhardt
2019 – jetzt Business Development Manager bei BASF Forward AM
2017 – 2019 Head of 3D Printing bei einem 3D Druck Service Bureau
2017 Universitätsabschluss im Fach Wirtschaftsingenieurwesen, Master of Science

Digitalisierung als Schlüssel für den Industriellen 3D Druck
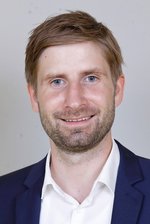
Tim Wischeropp, Abteilungsleiter AM Design, Fraunhofer-Einrichtung für Additive Produktionstechnologien IAPT
Abstract: Der 3D-Druck ist heutzutage in aller Munde und begeistert Anwender und Entwickler gleichermaßen. Allerdings stehen hohe Kosten einem wirtschaftlichen Einsatz in vielen Fällen entgegen. Der Vortrag gibt einen Überblick über aktuelle Entwicklungen und Herausforderungen im 3D-Druck und zeigt auf, wieso die Digitalisierung bei der Industrialisierung der 3D-Druck Technologien eine entscheidende Rolle spielen wird.
Studium des Maschinenbaus der TU Hamburg und University of Waterloo (Kanada). Seit 2012 in der additiven Fertigung in verschiedenen Positionen am Fraunhofer IAPT (ehemals LZN Laser Zentrum Nord) aktiv. Seit Anfang 2018 Abteilungsleiter für den Bereich Design und Qualitätssicherung am Fraunhofer IAPT.

Additive Fertigung von Mikro- und Nanobauteilen
Jochen Zimmer, Sales Manager, Nanoscribe GmbH
Konventionelle 3D-Drucker erreichen typischerweise Schichtdicken von einigen zehn bis einigen hundert Mikrometer, und vergleichbare minimale Strukturgrößen. Nanoscribes 3D-Mikrodrucker nutzen Femtosekundenlaser und Polymer-Fotolacke, um mit der 2-Photonen-Polymerisation (2PP) Schichtdicken und Strukturgrößen unterhalb von einem Mikrometer zu ermöglichen. Es lassen sich Polymer-Objekte bis zu einer Größe von einigen Millimetern drucken. Der Druck auf oder sogar in vorstrukturierte Objekte ist möglich, ebenso der Druck von optisch glatten Oberflächen, z.B. Mikrolinsen.
Nanoscribes 3D-Mikrodrucker werden in Wissenschaft und Industrie eingesetzt, in der gesamten Bandbreite vom Prototypenbau über Werkzeugbau bis hin zur Produktion.
In meinem Vortrag werde ich die Technologie vorstellen, und verschiedene Anwendungsmöglichkeiten anhand von Kundenbeispielen erläutern. Die Beispiele werden aus den Bereichen Medizintechnik, Mikrooptik und Mikrofluidik kommen.
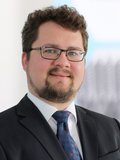
After his diploma (Dipl.-Phys.) from Universität Karlsruhe (TH), Jochen Zimmer worked on superconducting nanostructures at Karlsruhe Institute of Technology, gaining experience in direct laser writing and electron beam lithography. He received his doctorate for this work in 2013.
After that, Dr. Zimmer started working in the 3D printing industry, in product development for INDMATEC GmbH, and then in different sales engineering functions for Stratasys GmbH/Makerbot Division. Since 2017, he is a Sales Manager for Nanoscribe GmbH.
